Table of Content
The outdoor space typically consists of large decks that may wrap around the house, which extends the living space of the floor plan. This space can be used for anything from entertaining to relaxation. Before you start covering the roof with plywood, check to see if you need any additional backing or bridging blocks to hold the plywood. You don’t want any plywood sections to be loose or not secured to the frame. Just like the plywood on the floor, all plywood edges should land on the boards.

When working with concrete, you have a limited amount of time before it becomes hard. After concrete becomes harder, it’s very difficult to adjust or change its shape. So you will need to have your materials ready before mixing the concrete.
It has no external walls
Finally, the owner must obtain the necessary building permits from their local government. Without these key items in place, it would be impossible to start building an A-Frame house. Another advantage of a tiny A-frame is that they are relatively easy to construct. If you have some basic carpentry skills, then you should be able to build one on your own. However, if you’re not sure about your abilities, then it’s always a good idea to hire a professional contractor to help you out. Either way, building an tiny house is a fun and rewarding project that anyone can enjoy.
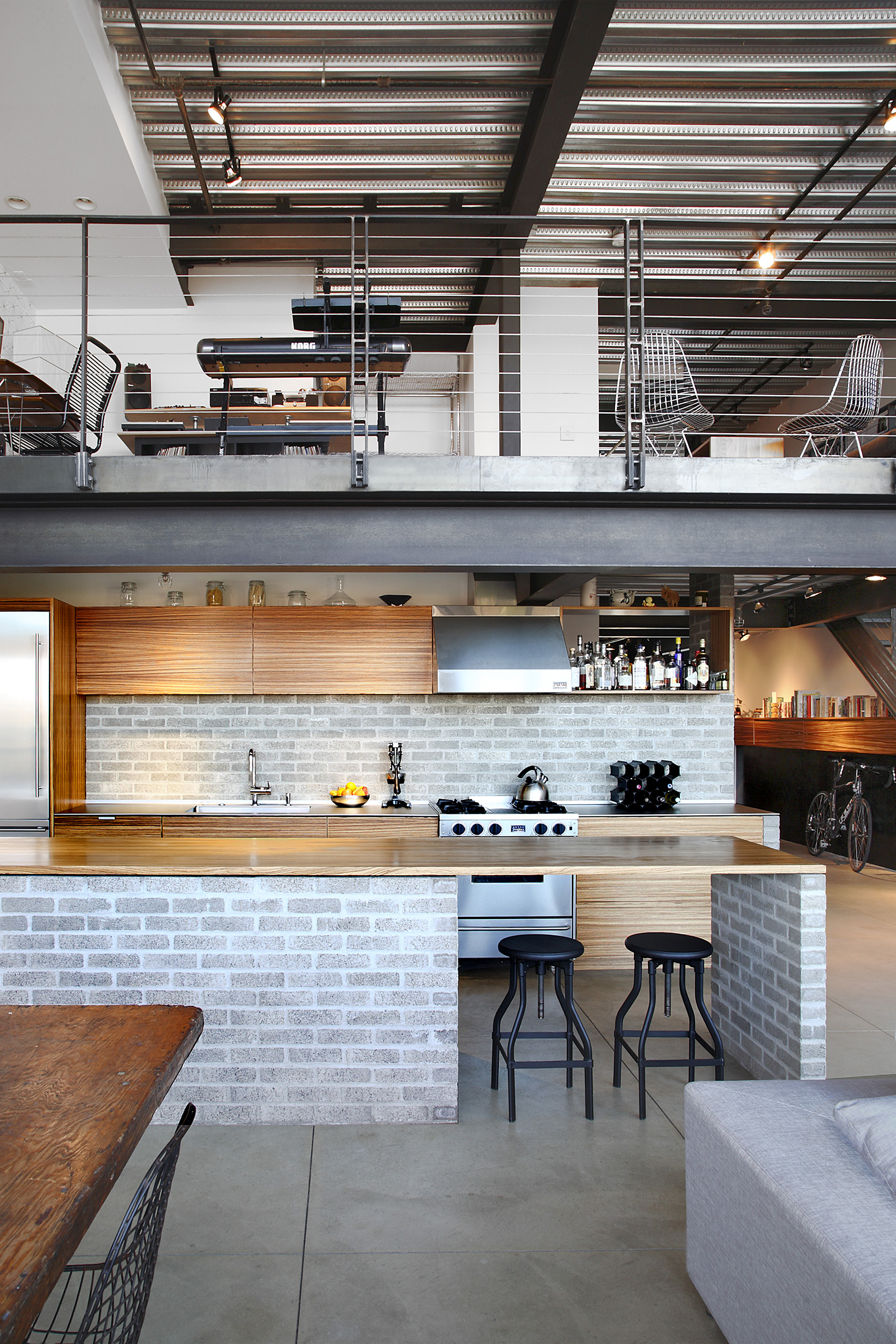
However, the length of the connections between construction components , is about 10% shorter than what would you would find in a regular house. Except for the front and back walls, there is no vertical external surface in the house. I love to create, design, repurpose, and fix anything that is broken at my house by doing it myself.
Plan: #126-1890
This 20-foot-per-side equilateral A-frame rests on tripled 2-by-10 pressure-treated beams supported by masonry block piers. The triangles, spaced 24 inches apart, are formed of 2-by-8 rafters joined at the apexes with plywood gussets and sandwiched at the bottom by pairs of pressure-treated 2-by-6 joists. The rafters of the end walls are doubled to provide a flush nailing surface for the exterior sheathing. The sleeping loft, reached by a ladder, is framed by a railing secured to posts and rafters. Knee walls along the sides of the cabin provide concealed storage areas. The stairs are set on concrete footings and are attached to the deck with metal framing anchors.
David Johnston has been developing green building programs for the last 10 years. Named one of the top 50 remodelers in the country by Remodeling Magazine in 1990, he developed the first green remodeling program in the country in Boulder, Colorado. He trains remodelers across the U.S. and is creating a national green certification program for the National Association of the Remodeling Industry.
Step 5: Clear the property
As many folks have mentioned, with the freeze thaw cycles, things are subject to some movement. There's a lot of frustration in making unneccsary trips and lugging materials, only to not be able to use them. Fortunately for me—and the cabin—there's a guru at the woodshop, by the name of Richard Scott! He's got a lifetime of experience and I am incredibly fortunate to have him impart some of his wisdom onto my projects.

If you want to build an A-frame house, you’ll first need to buy land zoned for residential buildings. The total cost for the build alone ended up being $10,632 CAD / $8,012 USD, not including land. Which is about $106 per square foot, as the cabin is basically a 10x10' box. Whether you’re looking to build a rustic retreat or the off-grid home you’ve long dreamed about, the A-frame cabin offers a simple, incredibly sturdy and comparatively low-cost option.
This one is subjective, but unfortunately the polycarbonate roofing that I had on my outhouse barrel did not last a season. We suspect hail was the cause of several holes and cracks in the relatively new roof, but it ended up being a wasted expense for us, unfotunately. The most major lesson learned is I should have gone bigger. Don't get me wrong, the cabin is awesome, but heck, an extra 5-10 feet in both directions would have been a game changer and made it a little more habitable. But to see a thing you built come to life is the greatest gift you can give yourself in my opinion. Well first it’s important to note labor was essentially free.
Then insert the metal post base in the center into the piers while the concrete is still wet. Before the concrete hardens, place the 4×6 beam into the metal post base spanning the piers. This will allow you to make any final adjustments to the metal base to line up with the 4×6 beam. Now dig out 14″ round and 24″ deep holes for the piers . Then take 12″ round concrete form tubes and cut 12 pieces to 24″ in length.
“These kits typically include all materials necessary to build an A-frame,” says Joshua Haley, founder of Moving Astute. And once you’ve purchased the land, you must go through the process to obtain a building permit from your local municipality. Building in a generous sky light will not only add even more natural light to the space, it’ll also allow for the perfect sky gazing opportunities come nightfall.
A building is basically framed in sections and the sections joined together. Despite the ebb and flow of the A-Frame house’s popularity over time, its charm has never wavered. It’s functionality, timeless aesthetic, and rich history shows that the A-Frame house is here to stay — or at least make another comeback in a few decades. For the best Prefab A-Frame kits, check out "9 Affordable A-Frame House Kits Available Worldwide." To learn the full history of the A-Frame house, check out, "The History of A-Frames in North America and Beyond."
The homes feature a triangular, custom fabricated truss system, a dormer window, and second-level living. But the more I dig deep into every aspect of it, the more I don't see why people should build a regular "cubic" house. In the TRIO series, the width of the living room is 6.2m ... That's a big plus you get for not having exterior walls.
The expenses vary according to location, making it impossible to calculate an overall average. The cost per foot of constructing an A-Frame cabin is around 20 to 30 percent higher than a typical eight or nine-foot ceiling with the roof falling on the top plate. There are other variables that affect pricing, but this ratio has proven to be accurate. Plan sets DO NOT include plumbing details, insulation, res-check or energy, calculations, and site plans. Each truss has three to nine parts based on the model and location of the floor plan’s truss.
Next, build the batter boards for the string lines to establish a more accurate foundation layout. Then pull and adjust the strings to the exact dimensions following the cabin plans. “And your square footage costs might reach $300 per square foot or higher if you need to partially or mostly rely on labor,” Sherin notes.

Finally, finish installing hardwood flooring, baseboards, a ladder to the loft, light switches, and any other fixtures and trim. Once the electrical and backing are installed, fill in the roof trusses with the insulation, including the walls of the dormers. When designing the house, see theInternational Residential Codefor wood floor framing that shows the joist and beam spacing requirement. This chart shows the maximum floor joist spans allowed for different lumber sizes and types of wood.
No comments:
Post a Comment